Pneumatic tools are powered by compressed air, providing exceptional precision and higher power-to-weight ratios than their electric or battery-operated power-tool counterparts. They are a popular choice for people working with high-power tools on a regular basis and for extended periods, including automotive mechanics, agricultural, industrial and construction workers, carpenters and other woodworking artisans.
Find out what air tools are used for, how simple the maintenance can be, and how to protect your pneumatic tools and extend their service life.
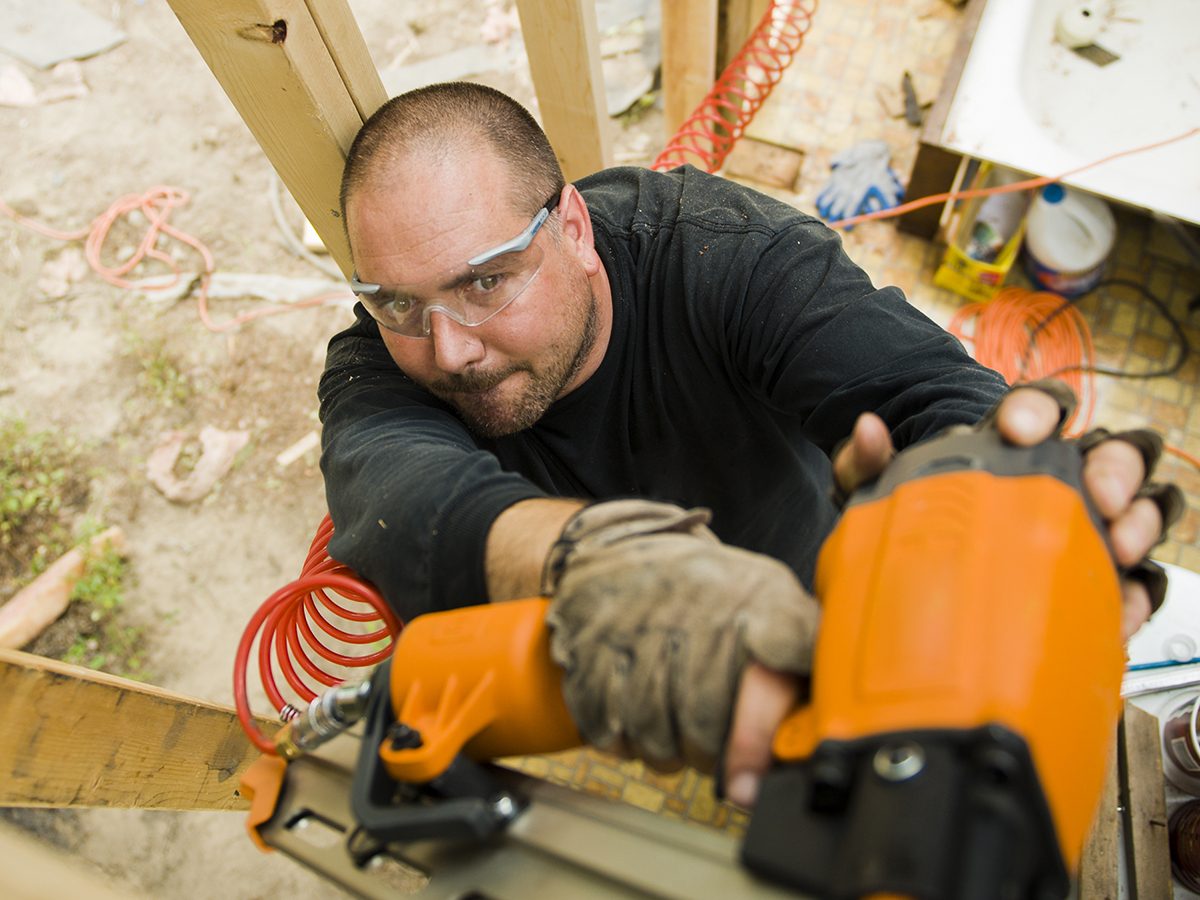
Common pneumatic tools:
- Grinders
Rotates a grinding wheel for grinding and cutting concrete, mortar, masonry and metals and smoothing out welds and polishing metals. - Impact Wrenches
Used to loosen and tighten bolts and nuts in automotive and construction applications where high torque is required. - Ratchet Wrenches
Used to drive screws and nuts when assembling furniture, working on cars, and repairing appliances. - Air Chisels & Hammers
Drives a piston that hits a chisel or punch that breaks or chips materials and is used to remove rust, break up concrete, and cut metal in mining, manufacturing, and demolition applications.
- Drills
Rotates a drill bit for drilling holes in wood, metal, and plastic. - Sanders
Rotates a sanding disk for sanding wood, metal, and plastic. - Nailers
A fast and efficient way to drive nails into wood and fasten materials together. - Staple Gun
Used to drive staples into wood, fabric, and other materials for upholstery and cabinetry work. - Blower
Uses compressed air to blow dust and debris away when cleaning cars, computers, workshops and other applications.
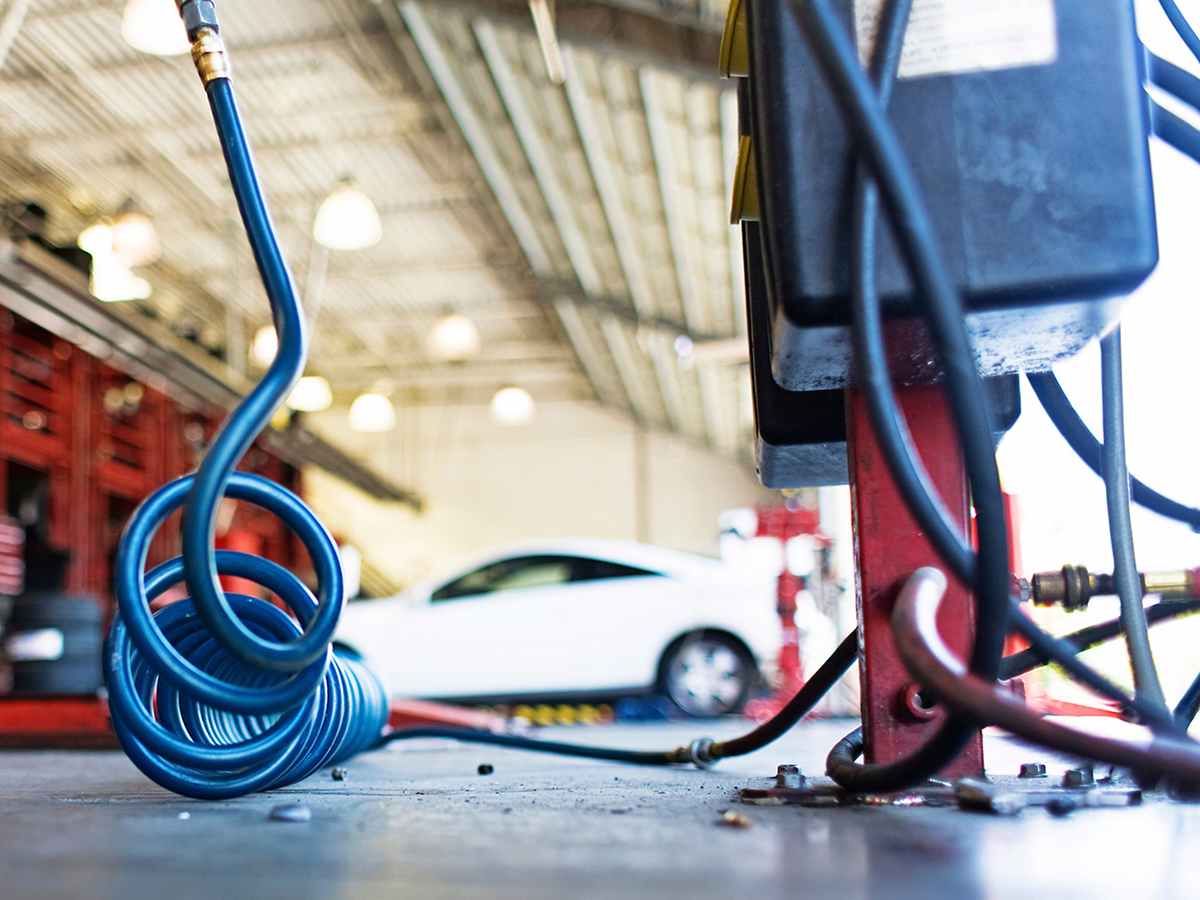
Air Tool Maintenance
Pneumatic tools contain bearings and motors, which must be lubricated to prevent premature wear. The simple solution is to apply 3-5 drops of AMSOIL Synthetic Air Tool Oil into the air intake before and after each use.
AMSOIL Synthetic Air Tool Oil effectively lubricates rotary and piston-type air-tool bearings and motors, while managing moisture and conditioning rubber and plastic seals and O-rings to help prevent leaks. It reduces wear and helps prevent corrosion and deposits to extend the life of your pneumatic tools and ensure they run smoothly, cleanly and reliably for many years.
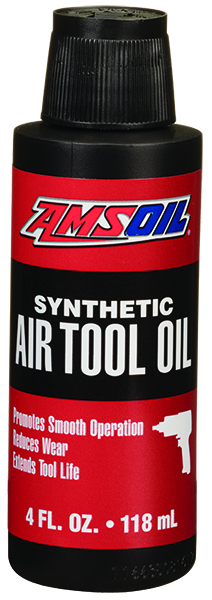
Comments
AMSOIL Technical Writer and 20-year veteran of the motorcycle industry. Enjoys tearing things apart to figure out how they work. If it can’t be repaired, it’s not worth owning.
Share: